Bio-heavy Oil and Diesel
01
Bio-heavy Oil Raw Material Production Sector- Definition of bioheavy oil : Heavy oil (energy) made mainly of vegetable and vegetable oils, palm oil, hot water oil, waste cooking oil, fatty acid me(E)ethyl ester mixed with various by-products, etc. and me(ethanol).
-
Energy source obtained by mixing various compounds with animal and plant oil, palm oil, hot water oil, waste oil, and various by-products, which are food
waste generated from human activities without obtaining raw materials from crude oil with severe environmental pollution, damage, or resource depletion
(less than 18 ppm sulfur oxide, less than 18 ppm nitrogen oxide, less than 50 mg/S㎥ dust).
(Quality Standards according to Notice No. 2019-36 of the Ministry of Trade, Industry and Energy) - The term “bioheavy oil for power generation” means a product produced in accordance with the quality standards of bioheavy oil for power generation as raw materials falling under any of the following items:
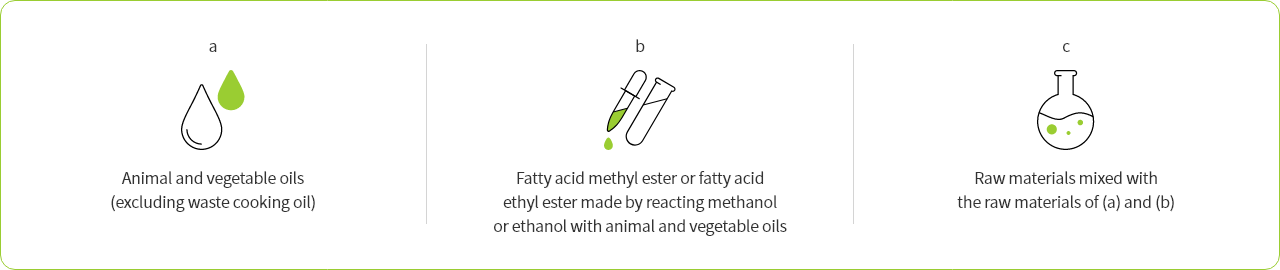
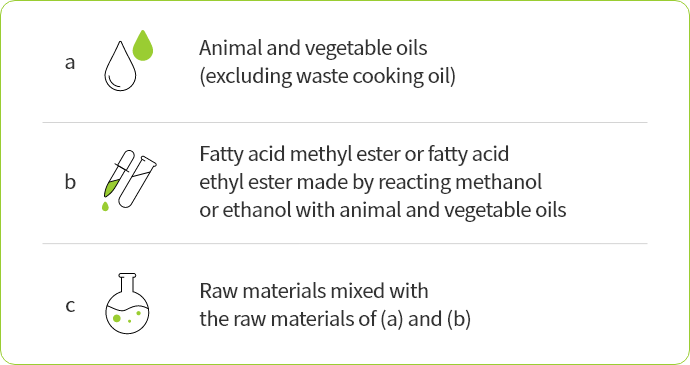
- Bioheavy oil is one of liquid bioenergy and alternative energy such as biooil and biodiesel, and it has the advantage of having low sulfur and nitrogen content because industrial waste or waste lubricant are not mixed.
- As a resource circulation eco-friendly energy, it is a substitute for bunker C oil, the most commonly used power generation fuel, and it is possible to supply domestic self-sufficiency (improvement of self-sufficiency) of raw materials and to secure supply stability.
- It has a large greenhouse gas reduction effect, can use existing bunker C oil production facilities as it is, emit 100% less sulfur oxide, 39% less nitrogen oxide, 28% less fine dust than bunker C oil, 70% less sulfur oxide, 16% less nitrogen oxide, and 33% less fine dust than bunker B oil.
- It is possible to secure overseas greenhouse gas emission rights and enter overseas markets by reviewing the feasibility of the carbon emission business.
02
The Field of Biodiesel Raw Material Production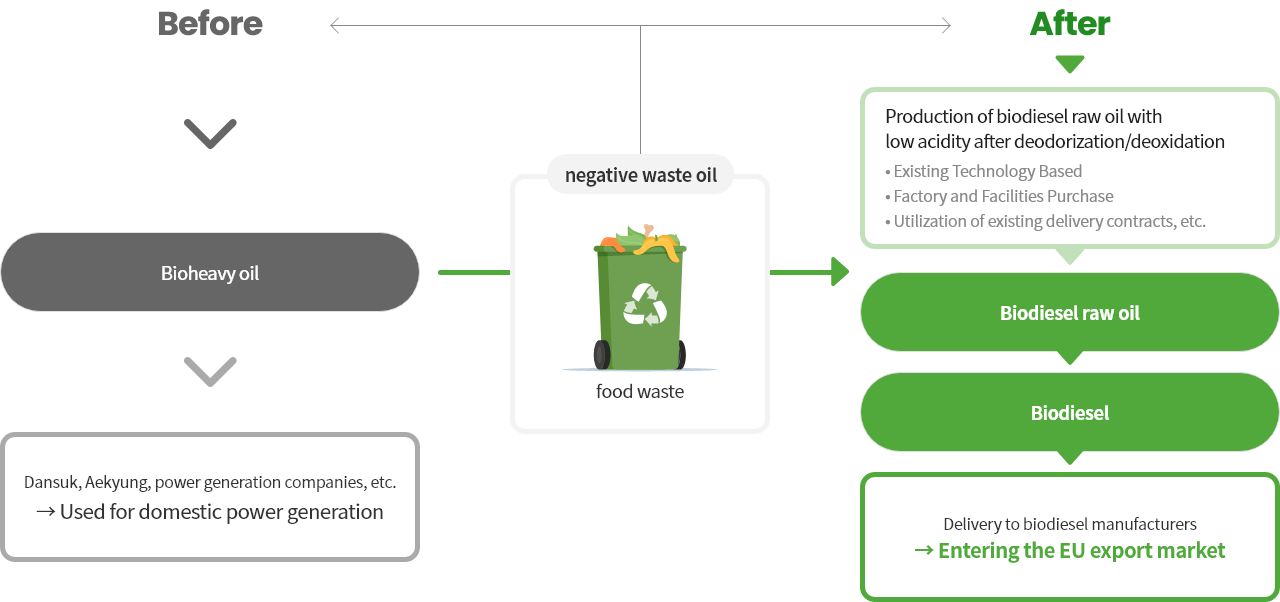
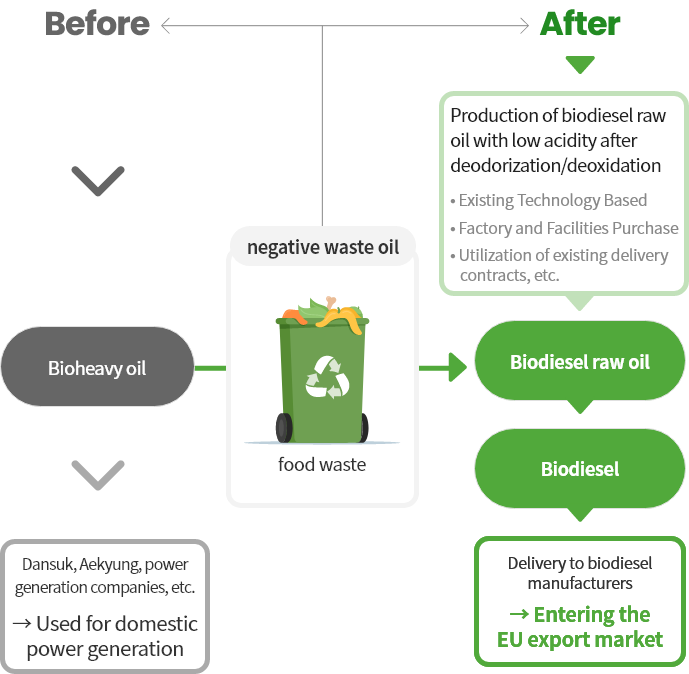
-
Description of biodiesel production process
- Dehydration, deodorization, and desorption processes : Dehydration and deodorization of oil and fat. Air is put into the bottom of the reactor to raise the temperature to 110°C and dehydrate to 0.05% or less of moisture.
- Deoxidation process (ester reaction) : Reaction temperature is raised from 110°C to 10°C per hour and ester is reacted at 150°C. Water/acid value is measured every hour and the reaction is completed at an acid value of 3 or less.
- De-glycerin process (purification step) : Remove the precipitate in the reaction tank and centrifuge to recover glycerin.
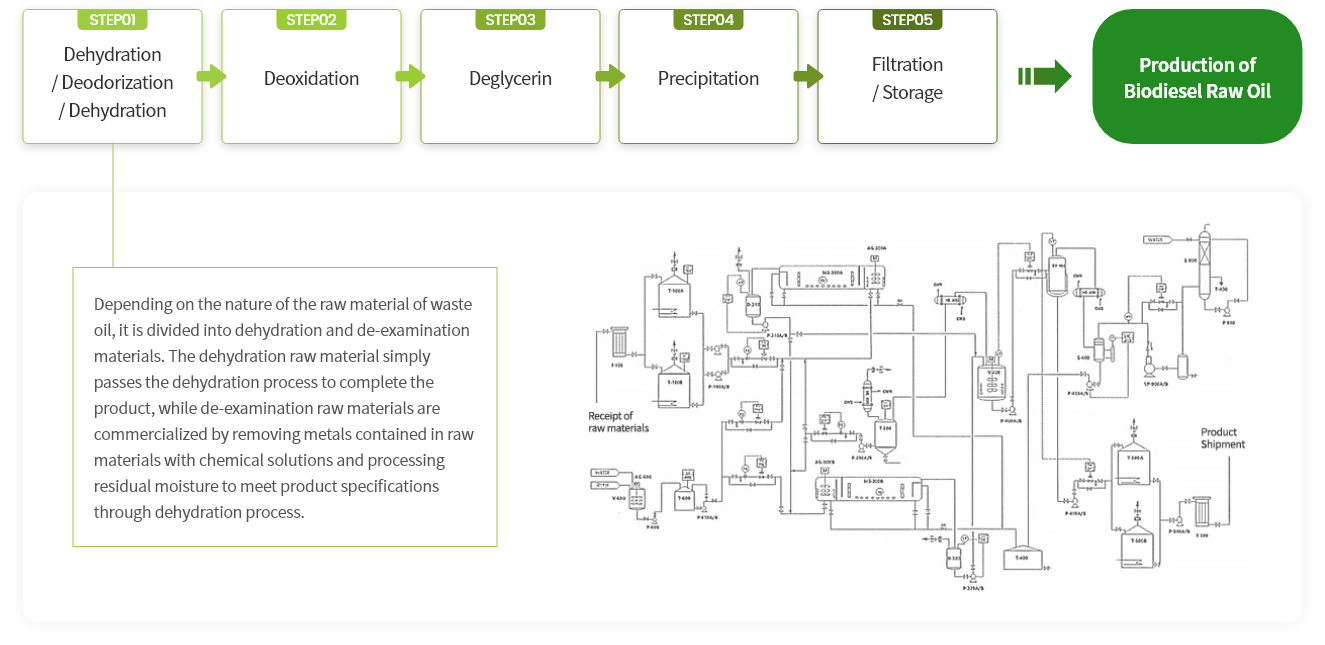
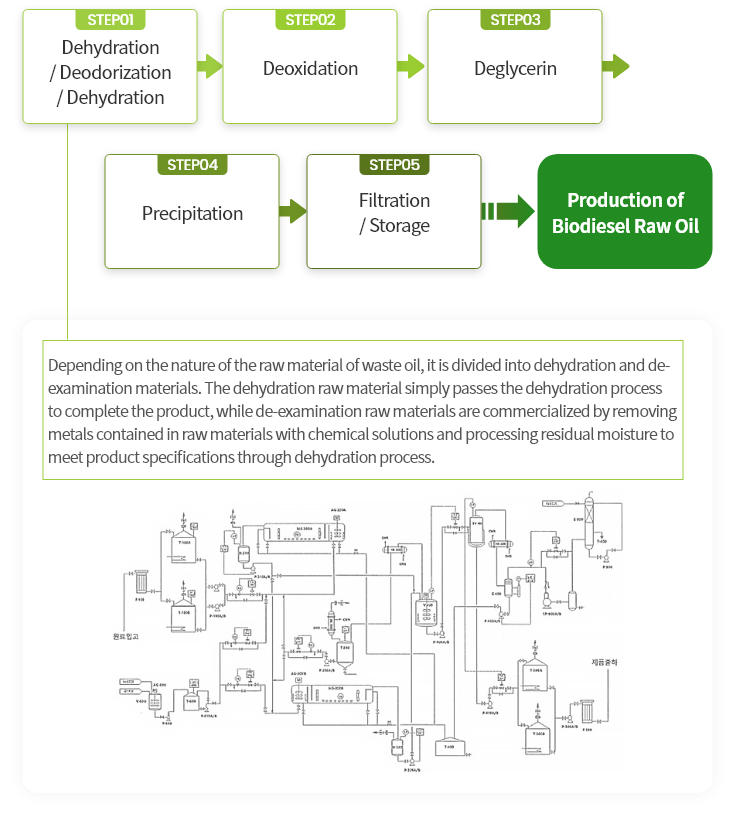